When we began manufacturing Allen Engineering suppressors, Ron sent us a bunch of knurled tubes to get started with our first batch of AEM5s. Something we noticed were the differences in the knurling from one tube to another. Since we get a lot of questions about the old and new knurling, we thought it would be a good idea to dive a bit deeper into the subject.
What is knurling?
Knurling is a process where a textured pattern is formed into a material using a tool with two wheels. There are many different knurling patters ranging from different depths, angles, and textures, however an angled knurl is most common. Typical angled knurls have a pattern opposite to each other that rolls with the work and the result is the criss-cross pattern you see pictured.
Knurling is much more art than a science. It can be a tricky process to do at times, let alone do consistently, especially on thin wall tubing that likes to warp with the tool rather than remaining in place like a solid part would. While things like the angle and width of the pattern are consistent, the depth and consistency are much more fluid. Minor fluctuations in a setup can yield drastic differences in the final result.
You can see in the picture with the knurling tool that even getting a consistent knurl across the part can be hard if the part varies in thickness or hardness.
Knurling is one of the defining, yet subtle features of an Allen Engineering suppressor. Its functional purpose is to give the suppressor texture to help tighten or remove it.
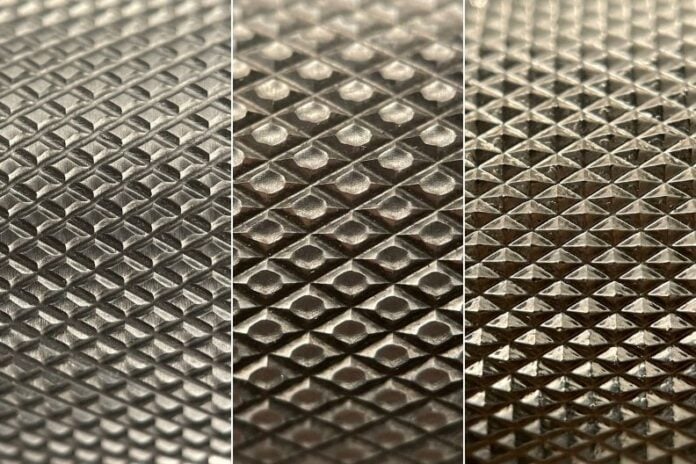
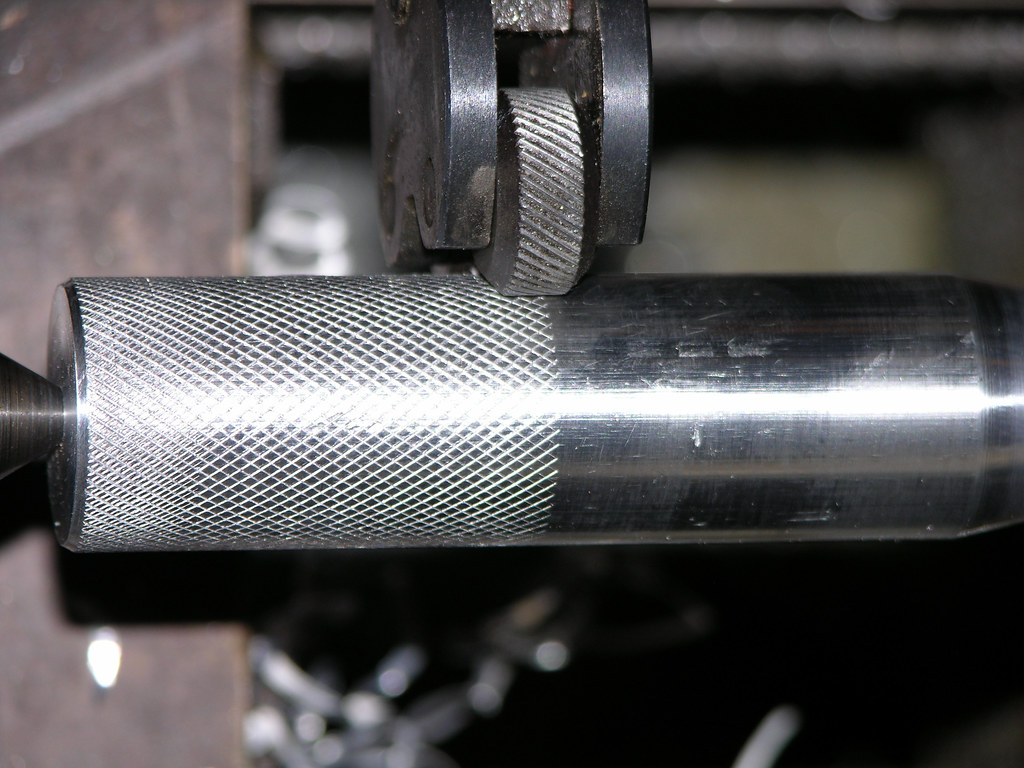
Why does my suppressor have this kind of knurling?
We have gotten many customers with an OPS/AE suppressor with unique knurling asking why why one suppressor doesn’t match another. Unfortunately there is no good answer to that. Typically, if the knurling is different than the standard design then the answer is that it was an accident. The way Phil and Ron knurled the suppressors was not always consistent and because the military were the primary buyers of the cans, the consistency was not relevant.
It wasn’t until they started selling suppressors to the civilian market when they started getting complaints about the inconsistent knurling. At one point Phil was so sick of people complaining about the knurling that he temporarily stopped knurling the suppressors altogether, which caused its own string of complaints.
Ron and Phil’s attitude towards the knurling at the time was that its form came second to its function. This attitude carried over to Allen Engineering when OPS INC shut down. So while Ron did reject a lot of knurled tubes that failed his QC and attempts were made to be more consistent, he did pass a lot of tubes with minor variations.
Why did you change the knurling?
The problem was that the old knurling was not consistent. This creates a lot of problems to both the manufacturing process and customer satisfaction, especially when someone purchases multiple suppressors. When we began manufacturing AE suppressors we knew we had to guarantee a consistent product to our customers. It was not an easy decision because we knew we would prompt a new set of complaints, but we believed that it provided a better product to the customer. The new knurling, while slightly deeper, provides better grip for the user while also making it easier for the knurling wheels to sync after the first rotation, eliminating double cut knurling you may have seen. We have also come up with new ways to be more consistent with the positioning and length of the knurled sections.
Below you will see the difference between the new knurling (deeper) and the old knurling.
Below you can see the many rejected tubes from Ron where it was accidentally double cut. The double cut knurl happens when the knurling wheels don’t synchronize after the rotation, leaving the appearance of a finer pattern. There are also many cans we jokingly call “1.5 cut”, where one wheel synchronized and the other didn’t.
Form over Function
Allen Engineering has always preferred function over form giving it a very utilitarian look. This is why many people jokingly refer to OPS/AE suppressors as “toobs”. They are still relevant today because of their performance, not because of their looks. Remember, the purpose of the knurling is to provide better texture to help tighten or remove the suppressor, not to look cool. So when we chose a knurling to make standard on the suppressors, we chose one that would do just that, while finding a way to do it consistently.
When Ron joined OPS INC in the 90s, he helped change the manufacturing process in numerous ways dramatically to increase the suppressors’ quality and consistency. The changes Ron made to the suppressors throughout the decades enriches the history of OPS/AE. We are currently working to document the history of OPS INC and Allen Engineering so each person can know the stories behind their suppressor, because how it was made marks a moment in the life of AE.
While we know that there will be plenty of people who will not like the change, we recognize that we cannot make everyone happy. When we showed Ron our version of the knurling and told him we were able to do it consistently, he expressed how much he wished he could have done it earlier. The legacy of OPS INC and AE is extremely important to us, and with Ron’s glowing approval we felt comfortable making this change.