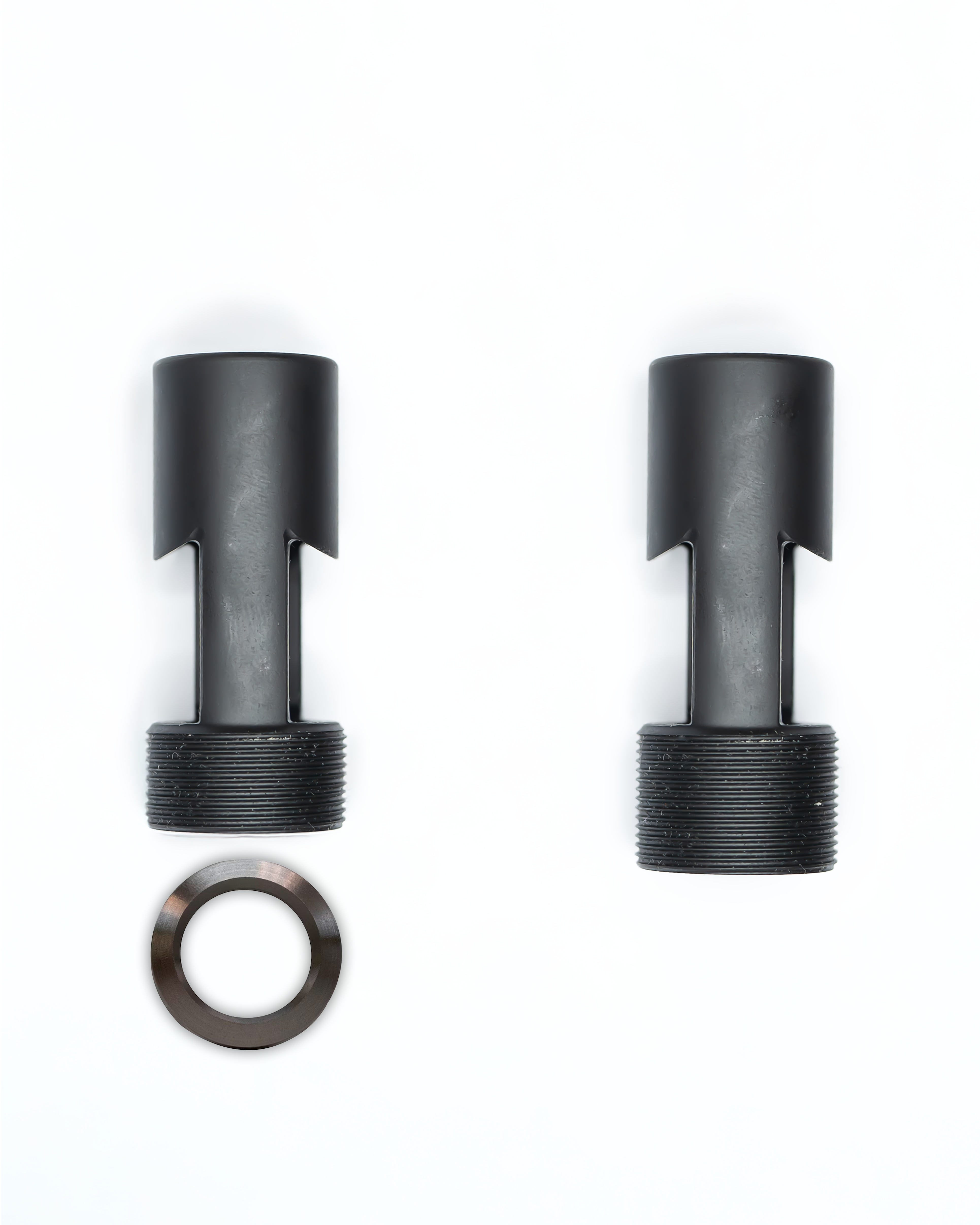
When shopping for an OPS/AE style brake many people ask, what is the difference between the short and long brakes? Simply, they are functionally the exactly the same, it just comes down to how you want to time your muzzle device. So if you are struggling figuring out which one will work for your setup, they will both work. The only difference is that one uses a crush washer and the other uses shims.
First it is important for you to understand how many turns it should take to mount your suppressor. If you haven’t read our blog post on that subject, please click here. In short, you should be getting 7-10 turns when mounting your suppressor. So if you use the wrong timing solution with the wrong muzzle device then you could cause your suppressor to require more than 10 turns or less than 7 turns to properly mount it.
To purchase an OPS/AE brake please click here.
Long Brake
This style brake has the longer external threads. The long brakes are available in 1/2×28 and 5/5×24. These brakes are meant to be timed with shims. Originally, all the brakes were the long variant.
Shims are extremely thin and do not typically push the muzzle device that far forward. This will keep the muzzle device in the correct position to accommodate the 7-10 turns for proper mounting. If you use shims with a short brake then you will most likely cause your suppressor to have less than 7 turns when mounting. This will likely produce carbon buildup on the internal threads of the suppressor.
Short Brake
This style brake has the shorter external threads. The short brakes are only available in 1/2×28 thread pitch. These brakes are meant to be timed with crush washers. Use of a crush washer was originally done by request of DoD, notably in the 12th Model (AEM5) suppressor on MK12 SPR.
I just heard all of you panic because you know you shouldn’t use crush washers on your suppressor muzzle devices. You are correct, with traditional mounted suppressor hosts you will want to avoid crush washers, but Allen Engineering suppressors don’t use traditional mounts. The key to the two-point mounting system is the use of a collar. The taper on the collar is what aligns the suppressor, so concentricity issues typically caused by a crush washer are not an issue here.
Since crush washers are thicker they will push the muzzle device forward and that is why they made a shorter brake. The short brake with a crush washer matches the length of the long brake.
If you use a crush washer with the long brake then you will cause your suppressor to have more than 10 turns when mounting. This will in turn cause the threads on your muzzle device will be exposed within the blast chamber. This will likely produce carbon buildup on the muzzle devices threads and prevent the removal of the suppressor.
3rd Party Muzzle Devices
Many 3rd party muzzle devices will attempt to replicate the thread length of the short brake. I say attempt because they often vary dramatically in thread length which can make it difficult to properly mount your suppressor. We recommend sticking with OPS/AE branded or collaboration muzzle devices.
Mix and Match
There are a lot of odd barrel and hardware combinations out there. Occasionally you may have a combination that helps you achieve the correct number of turns without using the traditional setups. For example, a short brake and a tapered gas block may let you mount a B length suppressor on even a 10.5″ barrel! While some setups are proven, a little creativity in your setup can help you achieve something unique. As long as you are getting the correct number of turns when you mount your can, you are good to go!